Unlock New
Possibilities
Next-Gen Features
Enhanced Performance
Redefining Standards

Dynaform - a complete sheet metal forming simulation software for die design and evaluation.
Dynaform is a general purpose sheet metal forming simulation software solution.
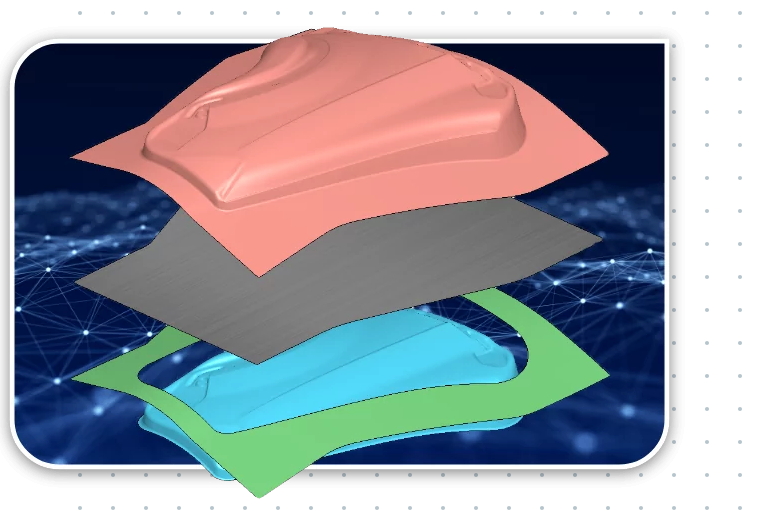
Total Materia
Announcing Our New Material Partner!
We are excited to announce our partnership with Total Materia. This collaboration integrates their vast material database in Dynaform, enhancing our ability to provide accurate and reliable material data solutions to our clients.Get access to over 540,000 materials and 25 million property records!
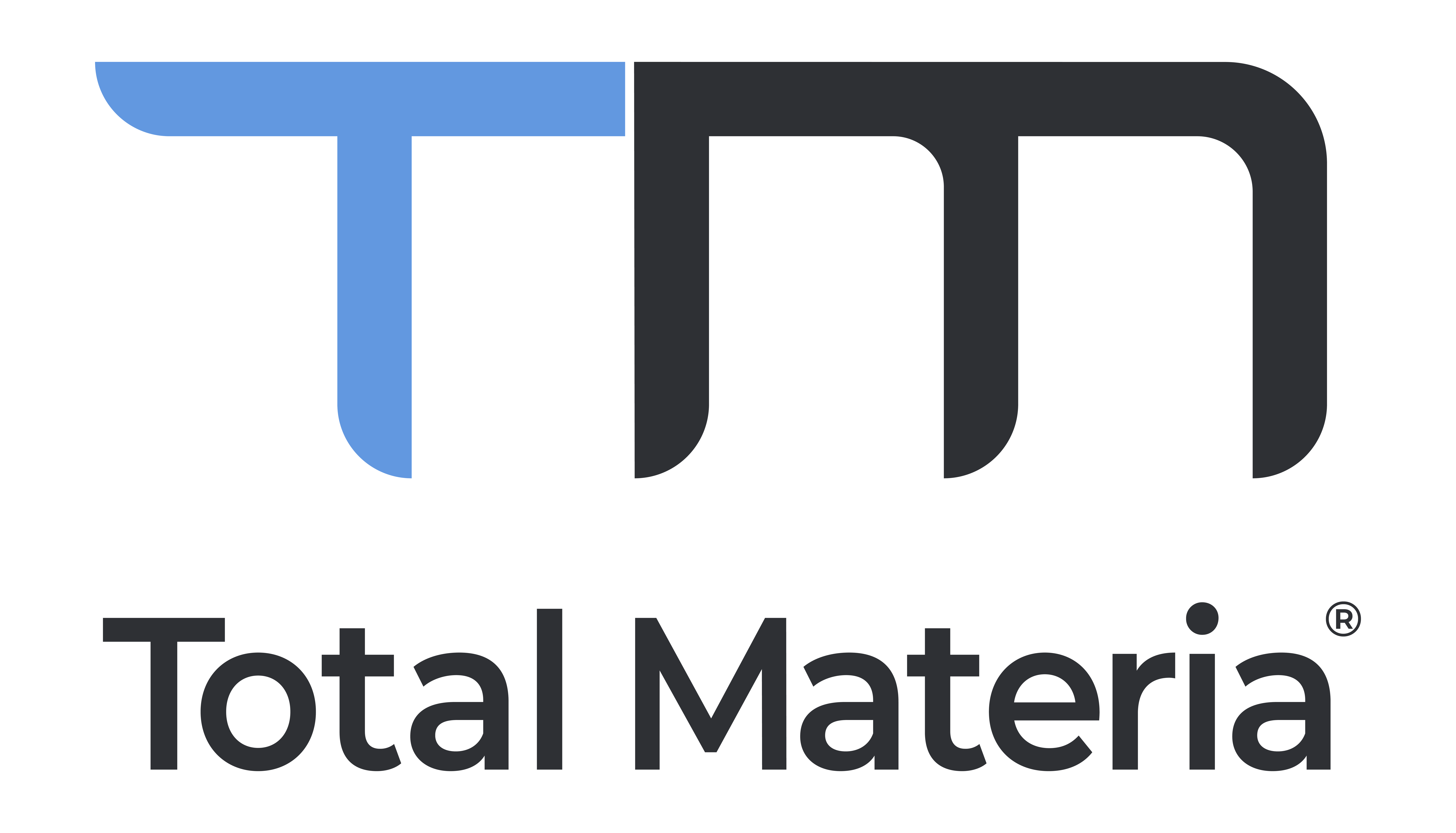
Dynaform Overview
Sheet Metal Forming Simulation Solutions
Dynaform® is a sheet metal forming simulation tool designed to improve all phases of the die development process. It allows an organization to entirely bypass soft tooling, reducing overall try-out time, lowering costs, increasing productivity and providing complete confidence in die system design. It also allows evaluation of alternative and unconventional designs and materials for an optimal solution. The most cost-effective and accurate solution available, Dynaform® is the clear choice among progressive organizations seeking to streamline the die analysis system. Dynaform® encompasses the entire die system process in one simple interface.
Key Features of Dynaform®
- Comprehensive Simulation: Encompasses the entire die system design process in a single interface.
- Accurate Multi-Stage Formability Analysis: Ensures the highest quality formed part and optimal manufacturing process.
- Solver: Includes Sigform, an explicit finite element solver for sheet metal applications which is fast and accurate. Dynaform® also supports the industry-standard LS-DYNA solver for reliable and robust simulations results.
- Cost Reduction: Bypasses soft tooling, reducing overall try-out time and costs.
- Productivity Boost: Increases productivity by streamlining the die development process.
- Design Flexibility: Evaluates alternative and unconventional designs and materials.
- Cost Estimation & Quoting: Guides through cost estimation and quoting for efficient project planning.
- Affordability: Leader in price-performance bracket, offering the most cost-effective and accurate solution available.
Modules
Blank Size Engineering (BSE)
A quick & easy process to check formability results & estimate manufacturing costs. Unfold 3D sheet metal designs, estimate blank size, reduce scrap.
BSE is a complete solution for accurately estimating blank size along with blank nesting for maximum material utilization, minimum scrap and piece costs. Using streamlined procedures, this powerful module allows the user to predict thinning, thickening, thickness strain, major prin. strain, min prin. strain, strain tensor & generate a forming limit diagram (FLD).
Key Features of BSE :
- Step-by-step Process Wizard
- Simple and Advanced unfolding mode
- Automatic Tipping
- Inner Fill
- Double Attached Parts
- Tailor Welded Blank (TWB)
- MSTEP (Modified One-Step) Solver
- Trimline estimation
- Blank nesting
- Batch BSE
- Batch Nesting
- Blank Development
- Nesting and cost estimation report in HTML and Excel format
- Quick feasibility study
BSE Sub-modules :
- Unfolding & Feasibility
- Nesting
- Trimline Estimation
- Assembly BSE
Die Face Design (DFD)
The Die Face Design module provides abundant tools for fast die surface design, including the binder design, addendum design and so on. It can be used to complete the design in the die quotation stage without special CAD software.
The Die Face Design (DFD) module offers an all-encompassing set of tools for quickly creating Line Die Layouts in multistage designs. These tools include Die Face creation, Forming Tool Design, Trimming, and Flanging Tool Design, along with the capabilities to modify the binder and addendum, make local feature adjustments, and efficiently evaluate the multistage setup. Users can fine-tune the binder, addendum, and other tools based on evaluation results, significantly enhancing the efficiency of Die Face design optimization.
Key Features of DFD:
Line Die Layout – Allows users to define multiple operations within the Die Face Design module. It includes features such as Detect Feature, Add Features, Add Processes, and Delete Process all of which are integrated to facilitate tool layout design directly within Dynaform.
Die Face Preparation – Surface edit tools aiding user in generation of binder and addendum.
Flange Tool Design – This function is used to create auto flange down, flange up tool, CAM Flange tool in Die Face Design module.
After the die face design is completed, the program automatically generates a tool for forming analysis to define the blank shape as well as the material and thickness, and quickly evaluate the designed die face using SigForm or LS DYNA solver.
Formability Simulation (FS)
The FS module facilitates the rapid development and validation of single-station, progressive and line die designs. It uncovers hidden problem areas and enables die designers to optimize designs based on accurate forming simulation results.
The FS module is designed for efficiency and ease of use. With a quick and easy interface, users can get started and setup their multi-station progressive die simulations. The user-friendly interface ensures a seamless experience, allowing for maximum productivity. The comprehensive material library includes standard material types, such as mild, high-strength, and stainless-steel materials, as well as new dual-phase steel, aluminium, and metallic alloys.
Dynaform has also partnered with Total Materia, an industry-leading material database provider. Total Materia provides access to over 540,000 materials and 25 million property records, powering the world’s most comprehensive solutions for materials selection, materials information management, ML-driven property prediction, compliance, and sustainability.
Whether you’re working with conventional or advanced materials, Dynaform’s Formability Simulation is equipped to handle your needs with precision and reliability.
Key Features of FS Module:
- Tree Structure Setup Process
- Simulation Data Manager
- Drawbead Shape and Library
- Drawbead Optimization
- Solid Blank Forming
- Coordinate System Manager
- Instant Section Cut
- Tata Steel FLD
- Springback Prediction
- Automatic Springback Compensation (SCP)
- Multi Stage Simulation
- Progressive Die Simulation
- Line Die Simulation
- Tonnage Prediction
- Face Reflection Analysis
- Stoning Analysis
- Skid Marks
- Special Forming Process
- Sheet Hydroforming
- Roller Hemming
- Superplastic Forming
- Stretch Forming
- Spinning Forming
FS Add-ons:
- Blank and Trimline Development
- Hot Forming
Die System Analysis (DSA)
The finite element approach to die system design is an efficient way to predict and resolve many stamping related concerns within the die production line. DSA simulations can help to streamline die system design from the analysis of scrap shedding and removal and die structural integrity, to sheet metal transferring and handling.
Die Structural Integrity (DSI)
DSI offers comprehensive tools to ensure the robustness and reliability of your die structures. Users can generate Finite Element Analysis (FEA) models of the die, define both operational and stamping loads and run simulation using both implicit and explicit approach to calculate the tool fatigue life. DSI helps predict the stress distribution, enabling users to optimize die design accordingly eventually saving material and handling cost.
Sheet Metal Transferring & Handling (SMTH)
SMTH offers advanced simulation capabilities to optimize metal transfer during manufacturing. This module enables users to simulate the entire transfer process, including the movement to die stations, between stations, and the placement of finished pieces on shipping racks. It predicts potential interference between the work-piece and tools, ensuring seamless operations. By utilizing stress and strain results, users can prevent damage during transportation, as well as during loading and unloading operations. Enhance your manufacturing efficiency and safeguard your products with our comprehensive transfer and handling solutions.
Scrap Shedding & Removal (SSR)
This module streamlines the modelling process for scrap, trim dies, chutes, and trim steel, ensuring efficient handling of waste materials. This module allows users to create precise trimming operations and shedding simulations, optimizing the entire workflow and minimizing production line stoppage.
Tube Bending & Forming (TBF)
Complete multi-stage tube forming simulation
Dynaform’s tube forming simulation now supports multi-stage tube forming, including tube bending, tube pre-forming, tube hydroforming, trimming, and annealing. The simulations can accurately predict failures like wrinkles, cracks, spring back, and feasibility of hydroforming. No matter what process you are using or which stage you are focusing on, you can easily find the function you are looking for.
- Auto-Tool Creation: Robust automated tool creation based on product geometry.
- Full-process Tube Forming: Key tube forming processes include features like bending, preforming, hydroforming, trimming, and annealing.
Bending table enhancements
Dynaform’s bending table now supports editing, inserting, and deleting operations. Users can now also import the bending table manually or automatically generate it from the center line. Our bending table generation algorithm improvements now serve to save users significant amounts of time generating tables.
- Enhanced Simulation: Simulate tube feeding, rotating, and bending simultaneously.
- Data Exchange: Enjoy seamless data exchanges with bending machines.
Next-generation hydroforming
Hydroforming in Dynaform now supports comprehensive die face design including tube end extensions, centerline auto calculating, quick generating of die separating lines, mesh model separation based on separating lines, and more. Instead of switching to CAD software to create the tools, users can finish almost all major FEA model preparation works in Dynaform.
- FEA Preparation: Finish motion definition, mesh editing, & more – all in Dynaform.
- Tools Generation: Generate both upper and lower tools quickly and easily.
Licensing
Easily choose the right type of License for you in 3 simple steps
Dynaform offers flexible licensing options to meet the diverse needs of our users. Explore our different license models, durations, access types, and geo-location options to find the perfect fit for your requirements.
License Term
- Perpetual License: Make a one-time purchase to gain indefinite usage rights to the software. This option is ideal for long-term projects and ongoing use.
- Annual Subscription: Suitable for short-term projects or for evaluating the software before committing to a longer term. Enjoy cost savings and continuous access throughout the year, offering flexibility and easy budgeting for your software needs.
Access Type
- Nodelocked License: Designed for individual use on a single workstation, ensuring that each user has dedicated access to the software.
- Network License: Enables concurrent access for multiple users within a network, making it ideal for larger teams and collaborative projects.
Geographic Location
- Local License: Restricted to a specific geographic location, making it perfect for teams operating within a single area.
- Global License: Provides access from any location worldwide, ideal for distributed teams and multinational organizations, ensuring seamless collaboration regardless of location.
Choose the licensing option that best suits your needs and get started with Dynaform software today. Still not sure which licensing option is right for you? Use the live chat option and let us help you!
Consultation Services
Your Partner in Engineering Excellence
We offer cutting-edge engineering services in the field of Sheet Metal Forming ranging from simple blank cost estimation to complex process setup & optimization. Our team of seasoned experts is dedicated to delivering customized solutions that meet your unique needs, ensuring precision and excellence in every project.
- Blank outline, nesting, part cost estimation
- Sheet Metal Forming Simulation
- Trim Line Development
- Forming Limit Diagram (FLD)
- Defect Prediction – Crack, Splitting, Thinning, Wrinkling
- Spring back Prediction
- Spring back compensation
- Process parameters prediction & Optimization
- Tool Fatigue Life Assessment
- Scrap Shedding & Removal analysis
- Part Transfer & Handling analysis
Benefits of Outsourcing Your Engineering Projects:
- Proprietary Software: Dynaform is our inhouse product for end-to-end die design and simulation which is widely accepted in the market and integrates with industry leading solver LS-Dyna.
- Cost Efficiency: Reduce operational costs by leveraging our expertise and resources, eliminating the need for extensive in-house teams.
- Access to Expertise: Gain access to a team of highly skilled engineers with specialized knowledge in various fields.
- Focus on Core Competencies: Allow your internal team to concentrate on core business activities while we handle the technical complexities.
- Quick Turnaround: Achieve faster project completion times with our dedicated team working efficiently on your behalf.
- Scalability: Easily scale your engineering capacity up or down based on project requirements without long-term commitments.
- Risk Mitigation: Rely on our expertise to ensure compliance with industry standards and mitigate potential risks.
Contact us today to learn more about how we can help you achieve your engineering goals!
Contact us
Our team of CAE experts are ready to discuss your needs and how we can help solve your problems through the right product, our engineering services, or in-client resources.
or call us at 1-248-729-3010