In today’s rapidly evolving manufacturing landscape, optimizing material utilization is no longer a choice but a necessity. As industries worldwide strive to strike a balance between sustainability and profitability, efficient […]
Read Full Article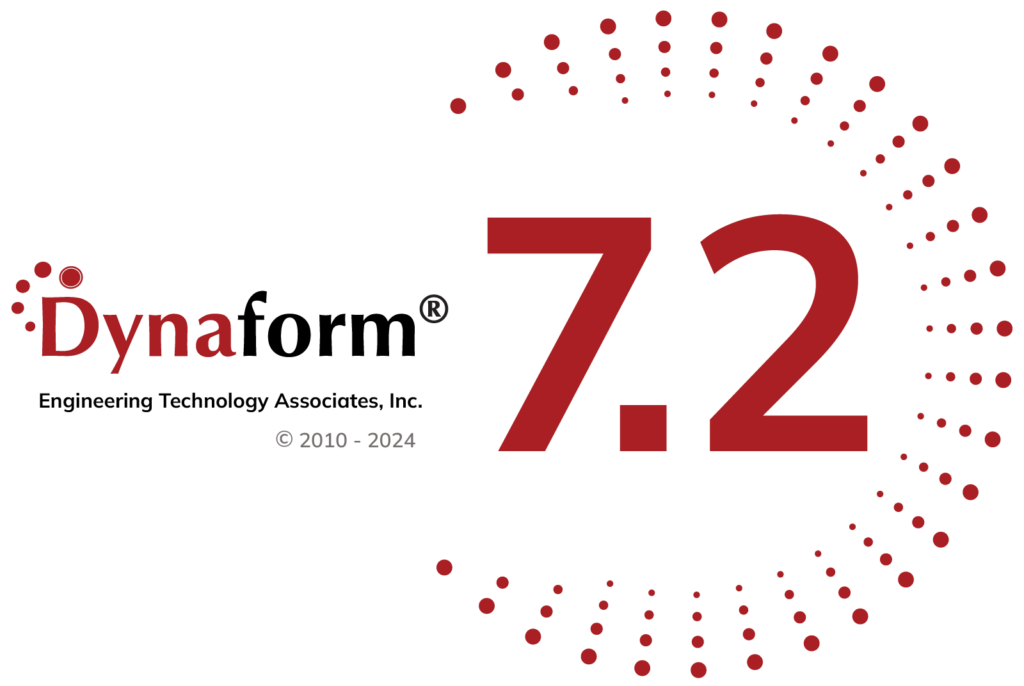

This will close in 0 seconds
This will close in 0 seconds
The gravity drop and transfer analysis feature has helped us minimize part deformation, ensuring better dimensional accuracy. It's been valuable in maintaining precision in our processes.
Feedback on Sheet Drop Test